CHACE HALL
UNIVERSITY PARK, PA
MOHAMED S. MOHAMED
MECHANICAL OPTION
Building statistics: part 1
GENERAL BUILDING DATA:
-
Building name: Chace Hall
-
Location and Site: Penn State’s Main Campus, University Park, PA.
-
Building Occupants: Penn State students
-
Building type: residential
-
Size: 48,515 SQFT
-
Number of stories above grade: 4, total levels: 5
-
Owner: Penn State University
-
Architect/Engineer: Clark Nexsen Architecture & Engineering http://www.clarknexsen.com/
-
Civil engineer: Sweetland Engineering & Associates Inc. www.sweetland-eng.com
-
Architectural, Mechanical, Structural, Fire alarm, Plumbing, Electrical, sprinkler-standpipe deisgn firm: Clark Nexsen http://www.clarknexsen.com/
-
Date of construction: 5/1/2012 to 7/31/2013
-
Cost: $94,100,000 (includes the renovation of the rest of South Halls; individual building cost not available yet)
-
Project delivery method: design-build
ARCHITECTURE:
Chace Hall was designed to exceed the standards of a typical Penn State residence hall. The architecture of the building looks modern and newer than many buildings and residence halls on campus, yet it still gives off the historic South Halls architectural theme. This is due to a historical requirement by the university that ensures that all buildings at the South Halls residence area look aesthetically similar. Some features that distinguish this design are the type of brick used in the building enclosure, the roof assembly with multiple brick gables, and the use of limestone on the bottom floor instead of brick veneer. This picture below shows some of those features.
The codes used to design Chace Hall are: International Building Code (IBC 2009), Americans w/ Disabilities Act Accessibility Guidelines for Buildings and Facilities (ADAAG) (July 23, 2004 edition), Pennsylvania Labor and Industry Fire and Panic Regulations, and Pennsylvania Labor and Industry Uniform Construction Code.
When it comes to construction at University Park, Penn State has its own design and construction standards that must also be followed. This standard is divided using the Construction Specification Institute's MasterFormat - 2004 edition. Finally, since Chace Hall is located on the University Park campus, the zoning area is a University Planned District (UPD).
BUILDING ENCLOSURE:
Chace Hall’s building enclosure is similar to many of the new buildings on campus. The façade contains a curtain wall to allow sunlight into the building. The other major exterior walls are mainly composed of brick veneer, limestone, and double glazed clear glass windows. The roof at Chace Hall is a typical assembly, consisting of structural trusses, metal deck, ply wood, underlayment and covered with synthetic slate shingles.
SUSTAINABILITY:
Chace Hall was designed with potential to achieve LEED Silver but only reached LEED Certification. The main sustainable measures taken in this project: reduction in water consumption, recycled and renewable building materials, savings in energy consumption, low VOC finish materials, construction waste management plans, and day-lighting.
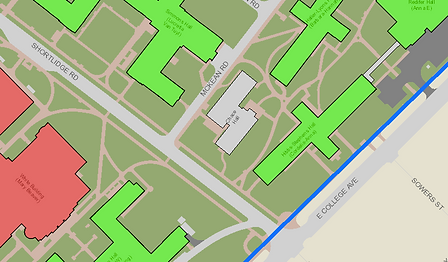
Building statistics: part 2
Mechanical System:
Designed by Clark Nexsen, Chace Hall’s mechanical system consists of several components that serve the cooling, heating and ventilation demands of the building. Heating and cooling are mainly done by Fan Coil Units (FCUs) that are located in most of the building’s occupiable spaces. There are 9 different types of Fan Coil Units in the building, where the ones that serves the bedrooms are 2-pipe units and the rest are 4-pipe units. The 2-pipe units can only heat or cool at a time, which typically depends on the season. On the other hand, the 4-pipe units can both heat and cool all year round. The building is connected to Penn State’s chilled water plants, where the chilled water running through the building come directly from one of the plants. Furthermore, the building is also connected to Penn State’s steam plant, where steam directly goes to the two steam to water heat exchangers located in the ground floor mechanical room. Due to this process, hot water can flow through the pipes to the FCUs and heat up the building. Furthermore, the mechanical system has 2 ductless split systems that serve the building’s telecom and elevator control rooms. In addition, an electric wall heater near the outdoor air intake is utilized.
An Energy Recovery Ventilator (ERV) is another major part of Chace Hall’s mechanical system. This 15 HP system is responsible for providing fresh outdoor air to the occupants and meet the building’s ventilation requirements. This 100% outdoor air unit also uses campus’ chilled water and steam to cool and heat outdoor air. It also has an energy recovery wheel, where the energy from the building’s exhaust is used to cool or heat incoming outdoor air. The unit has motorized dampers, different types of sensors, control valves and variable frequency drives (VFDs) that are directly connected to the building’s automation system. As one of the residence halls at Penn State University’s University Park campus, Chace Hall is a part of the university’s building
automation system network, the Automated Logic Control (ALC) system. This advanced system ensures that the officials at Penn State’s Office of Physical Plant (OPP) know about any failures that may occur in the system, allowing them to take the right measures to maintain the occupants’ safety and comfort, as well as protect the expensive mechanical equipment. Finally, the mechanical room piping plan below shows the flow of chilled and hot water to the different equipment.
Construction Management:
Chace Hall, a new 48,515 SQ FT residence hall on Penn State’s University Park Campus, was a part of the South Halls’ Renovation Project. This project also included the renovation of eight residence halls and Redifer Commons, South Halls’ dinning commons. The Barton Malow team spent around 15 months building Chace Hall along with carrying out renovations to the other halls and commons. The building’s delivery method was Design-Build, where great collaborations between Clark Nexsen (engineer) and Barton Malow (contractor) occurred to finish this project. This particular delivery method was chosen to decrease the time of construction and make the renovated residence halls and Chace Hall available to students before the Fall 2013 semester starts. As a result, the project was finished on July 31st, 2013, only 3 weeks before classes resume.
Lighting System:
A lot of lighting design was carried out by Clark Nexsen to ensure the resident’s optimal comfort. The residence hall’s bedroom and lobbies both have 10 Fc (Footcandles) as their average illuminance guideline. The luminaires in the bedrooms and staff lounge have 2 ceiling recessed 48W/120V linear fluorescent tubes (F28T8), with dimming capabilities. In addition, the student lounges/lobbies, corridors, kitchen, showers, toilets, stairs and vestibules are all equipped with ceiling recessed 1W/120V LED lighting. The building’s total lighting load sums up to 18,300 Watts which gives off a Lighting Power Density (LPD) of 0.38 W/SQ FT, as shown in the table below. Finally, all areas are equipped with occupancy sensors, where the lights will automatically turn off if the space is unoccupied.
Electrical System:
Chace Hall’s electrical supply comes directly from Redifer Commons, where the main electrical supply for all of South Halls is located. The building has a direct connection to the main switchgear in the commons that consists of 2 sets of (4#350, #1 G) wires in 4”C each, with a capacity of 225 KVA. In addition, the building has a connection to an emergency distribution panel, also located in the commons, that consists of (4#4/0, 4G) in 4”C.
Structural System:
The building has a steel structure that consists of wide flange beams and columns as well as hollow steel structure (HSS) members for the building’s braced frames. The beams and columns are generally W21x57, W18x40, W16x45 and W14x82 members, where the framing consists of HSS5x5x1/2, HSS6x6x3/8, HSS5x5x1/14 and HSS5x5x3/16 members. The typical above grade floors are made of 3.5” lightweight concrete on 2” deep composite steel deck (unshored construction) with a total minimum slab thickness equal to 5.5”. The slab is also reinforced with 6x6-W2.1xW2.1 WWF, that is placed ¾” clear of top of slab, fully supported. The roof frame consists of a 1 ½” wide rib, 20 gage, steel roof deck on cold-formed steel trusses (4’-0” UON spacing), supported on structural steel framing.
Telecommunications System:
All of Chace Hall’s telecommunications connections come from Redifer Commons. Coaxial trunk cabling, furnished and installed by Comcast, is responsible for providing the building with a CATV connection. Fiber optic cabling and voice cabling, furnished and installed by the owner, are responsible for providing the building with data and voice connections. The building is also equipped with WIFI routers for the occupants’ convenience.
Transportation System:
Chace Hall has 1 elevator that services the entire building from the ground floor to the fourth floor. The elevator is compliant with handicap accessibility codes.
Fire Protection System:
The residence hall has an automatic sprinkler system, a standpipe system, portable fire extinguishers (Type 2A, 1 per 600 SQ FT), automatic fire alarms, and visible manual fire alarms. The construction of the shafts and stairs are 2-hour rated fire barriers, where the sleeping room separations, most of the floors and corridors are ½ hour fire rated partitions.

